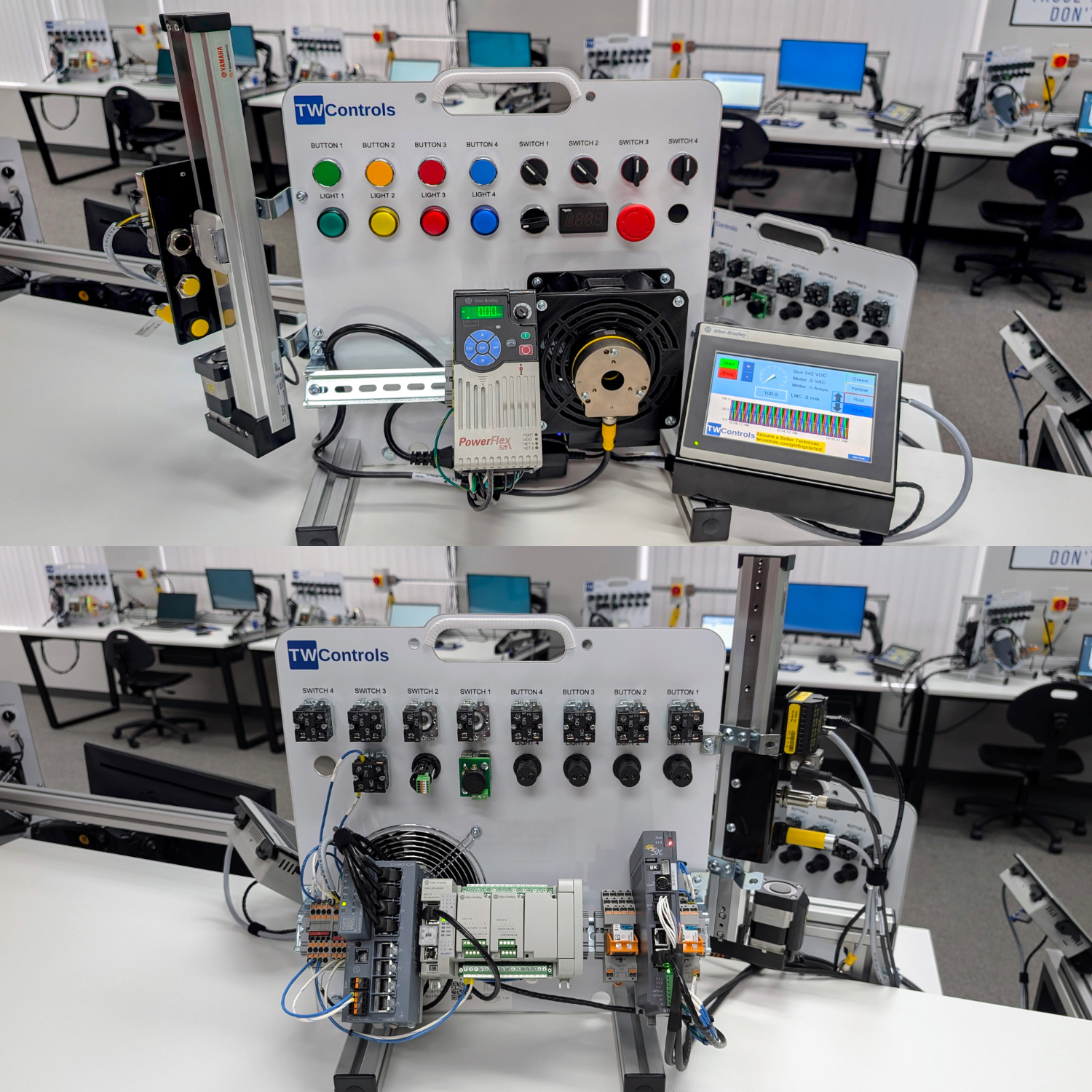
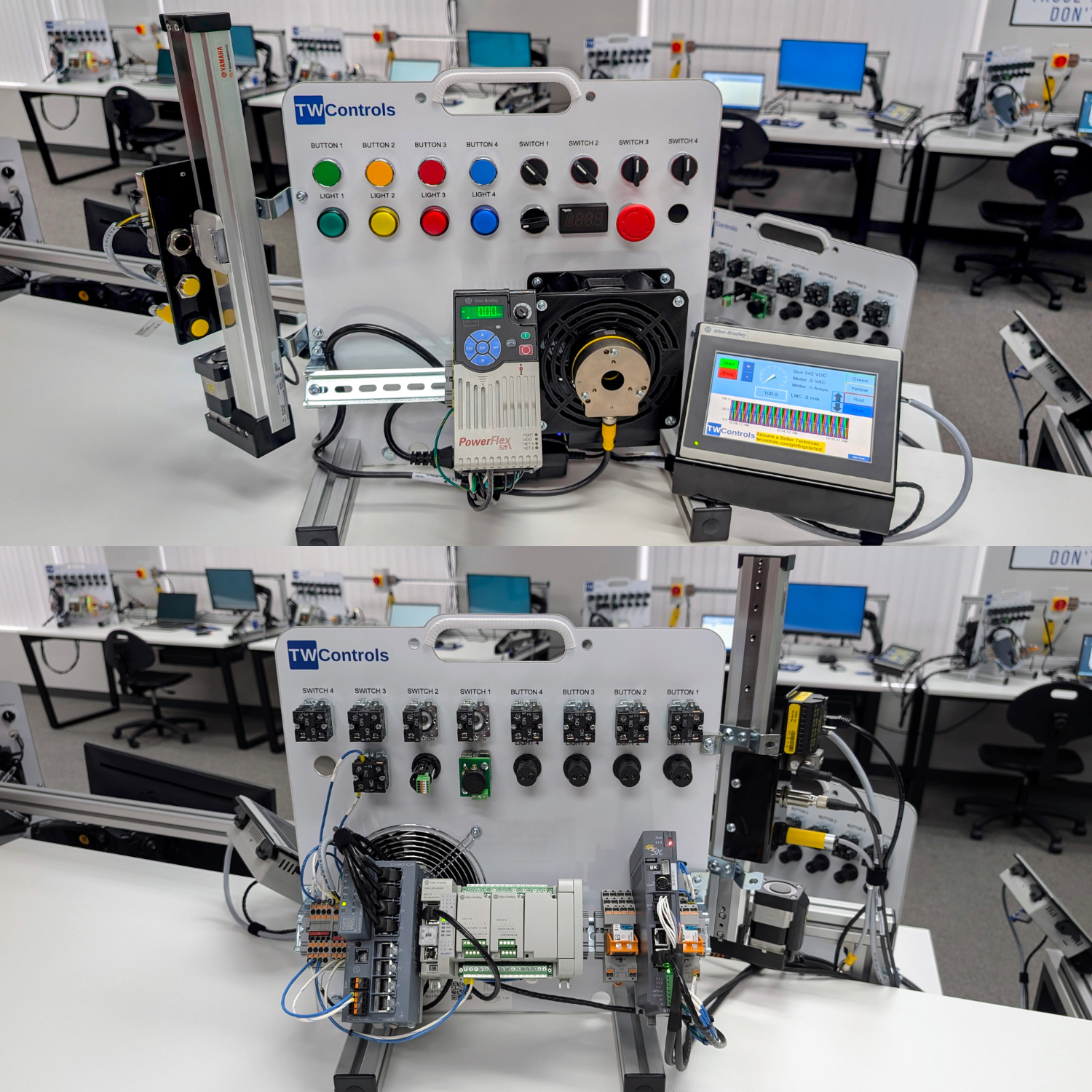
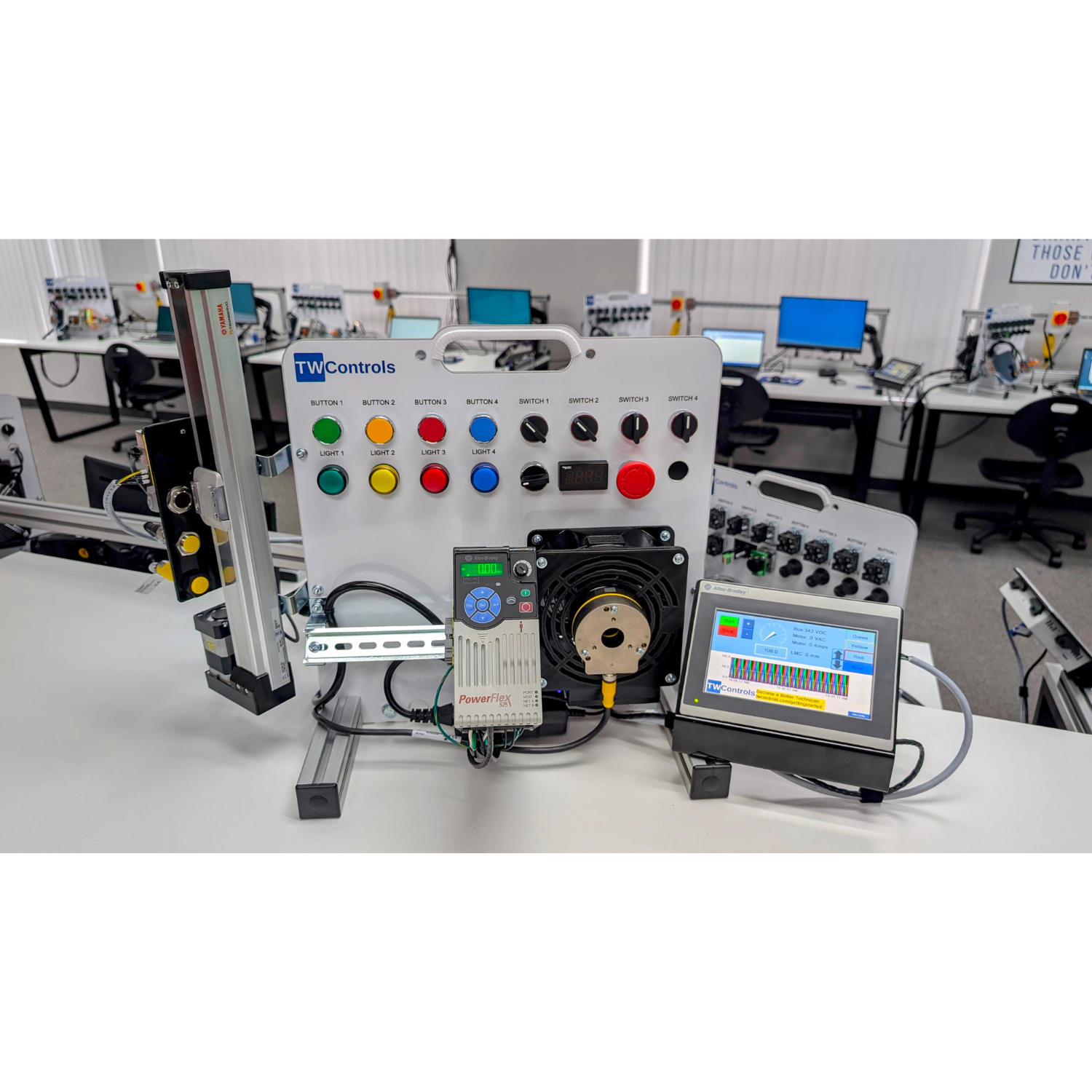
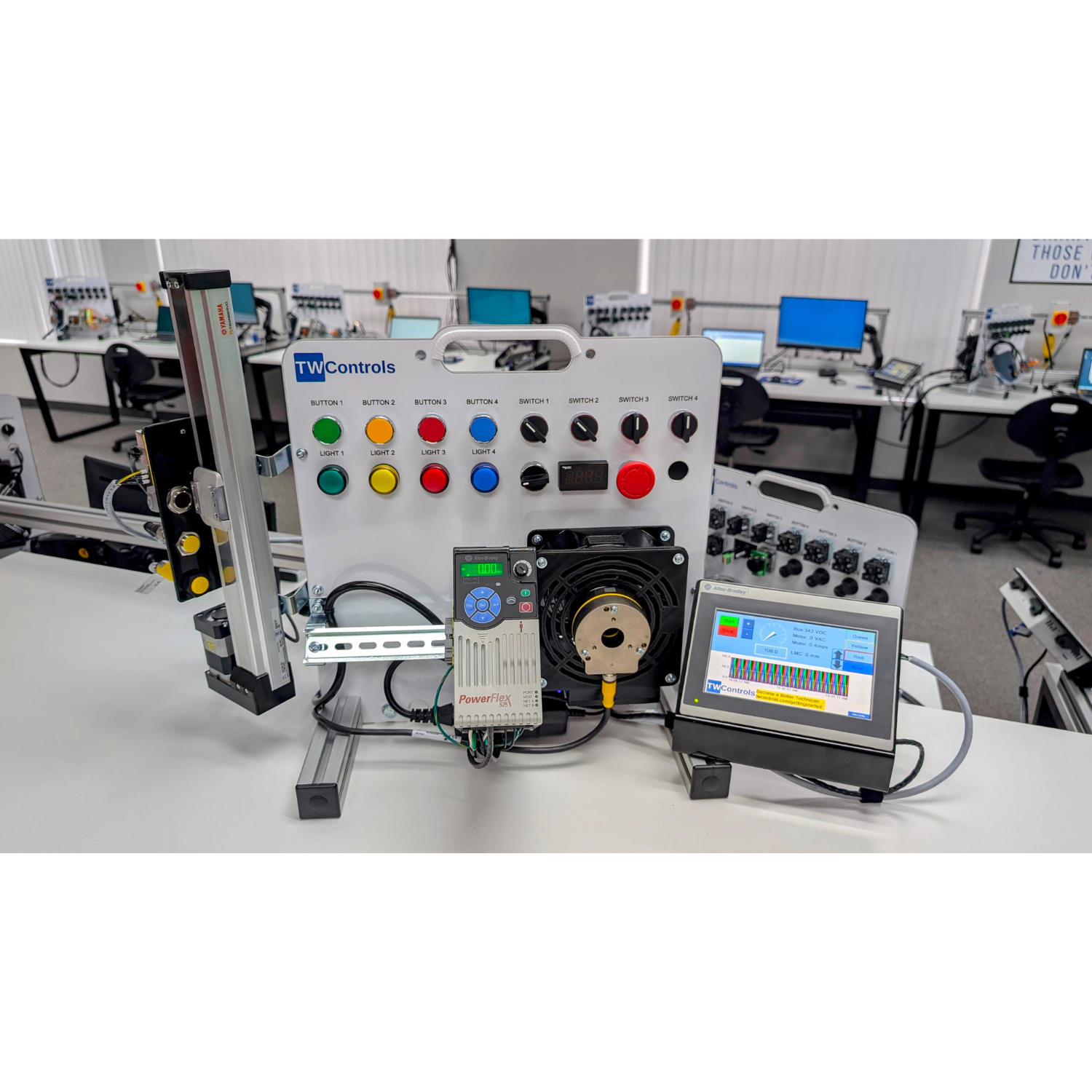
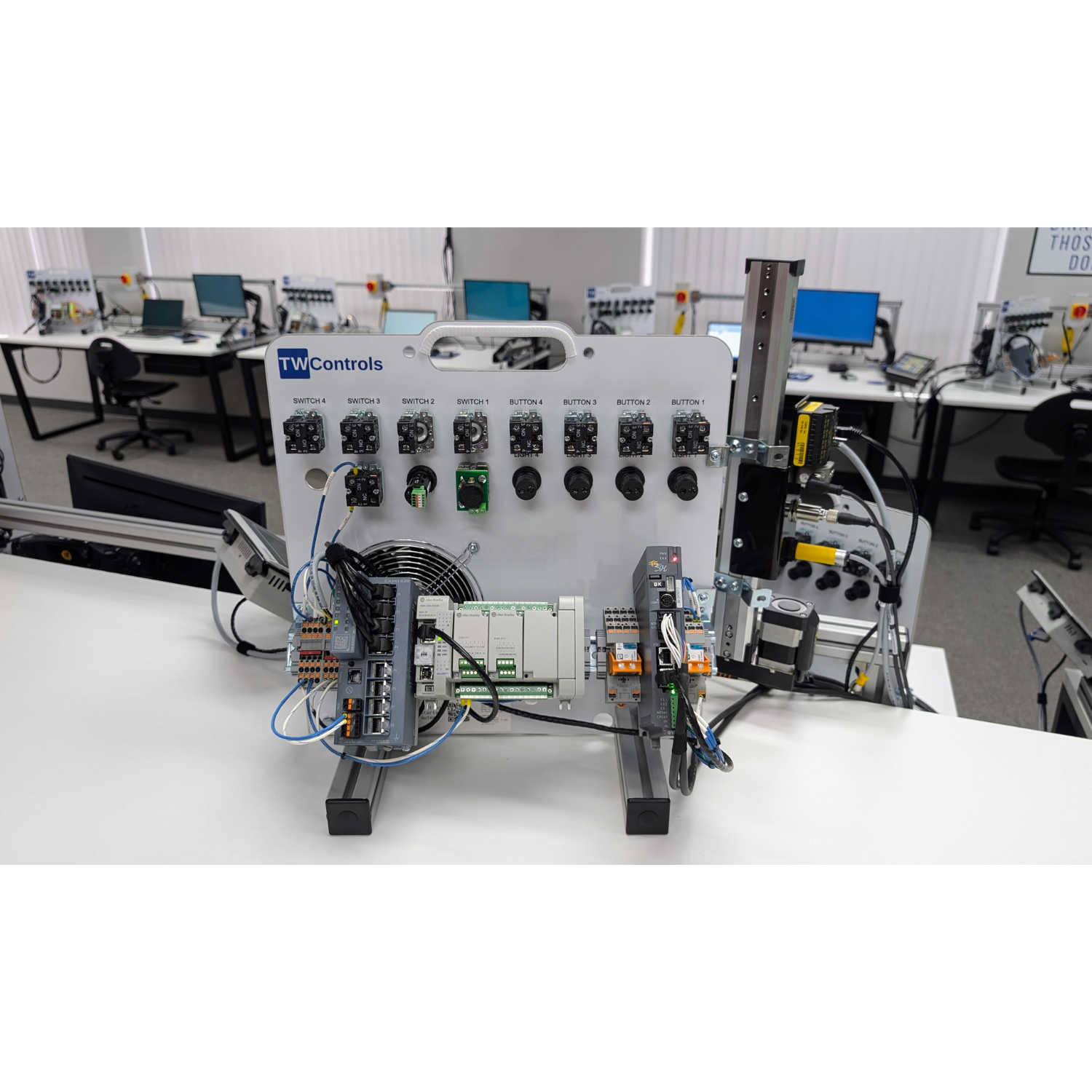
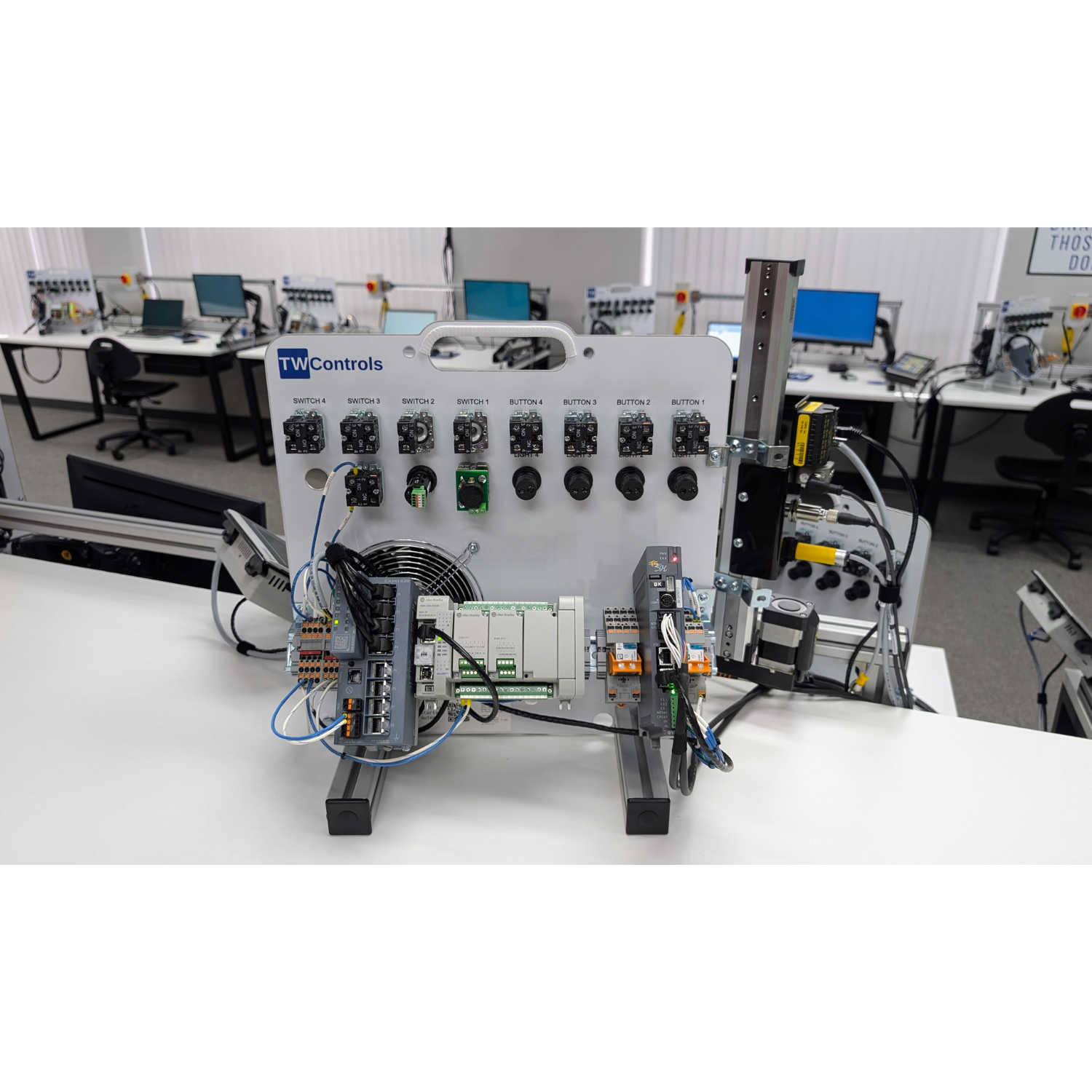
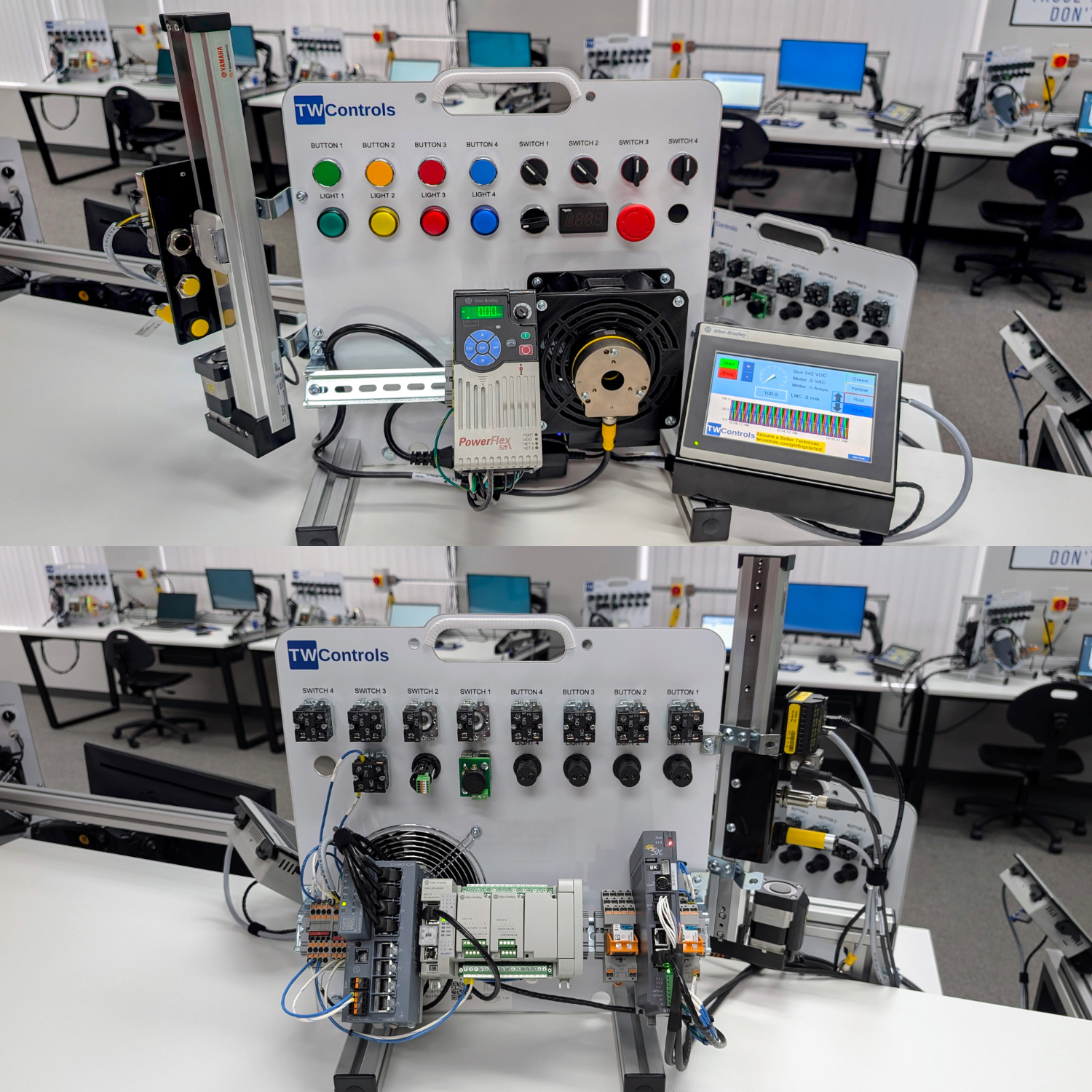
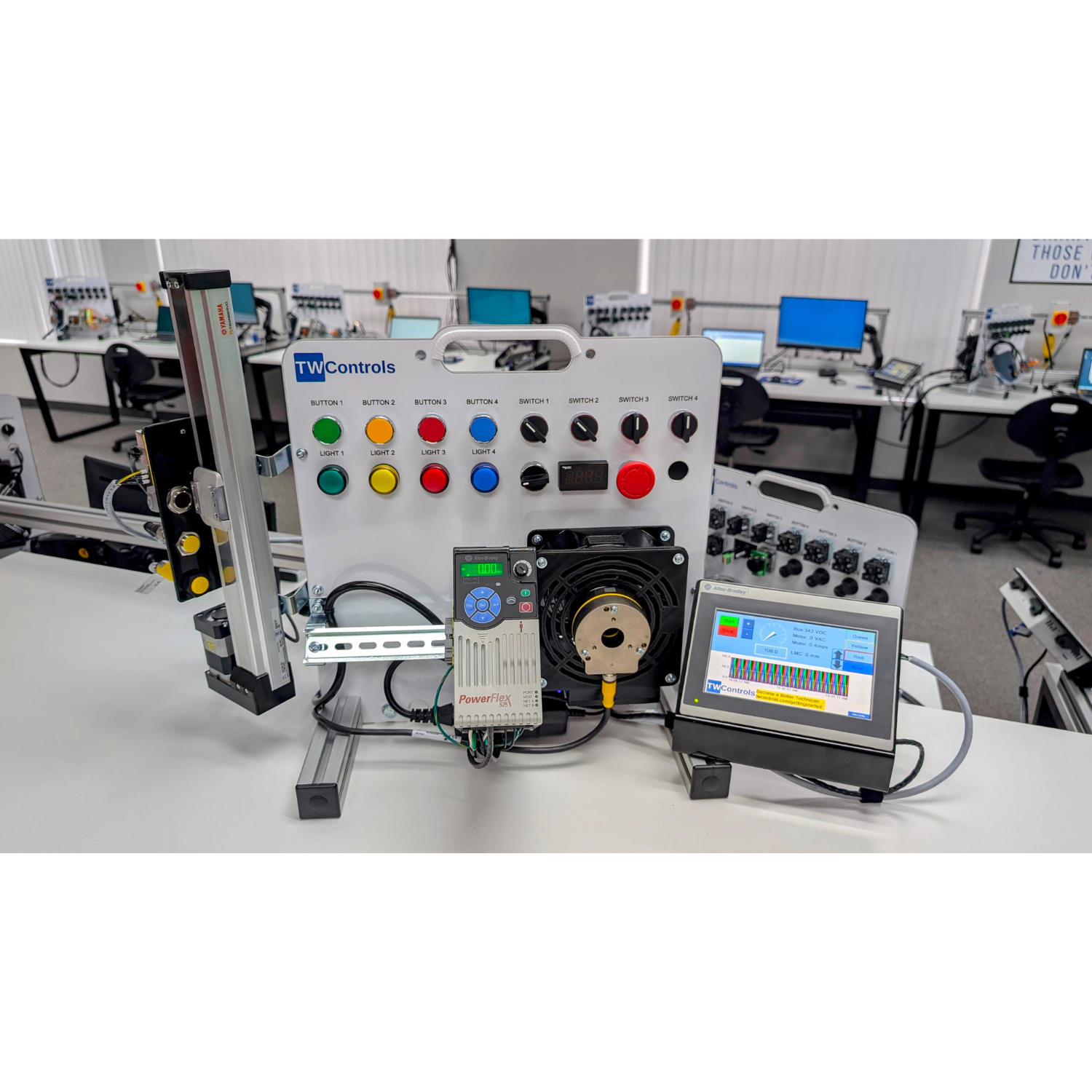
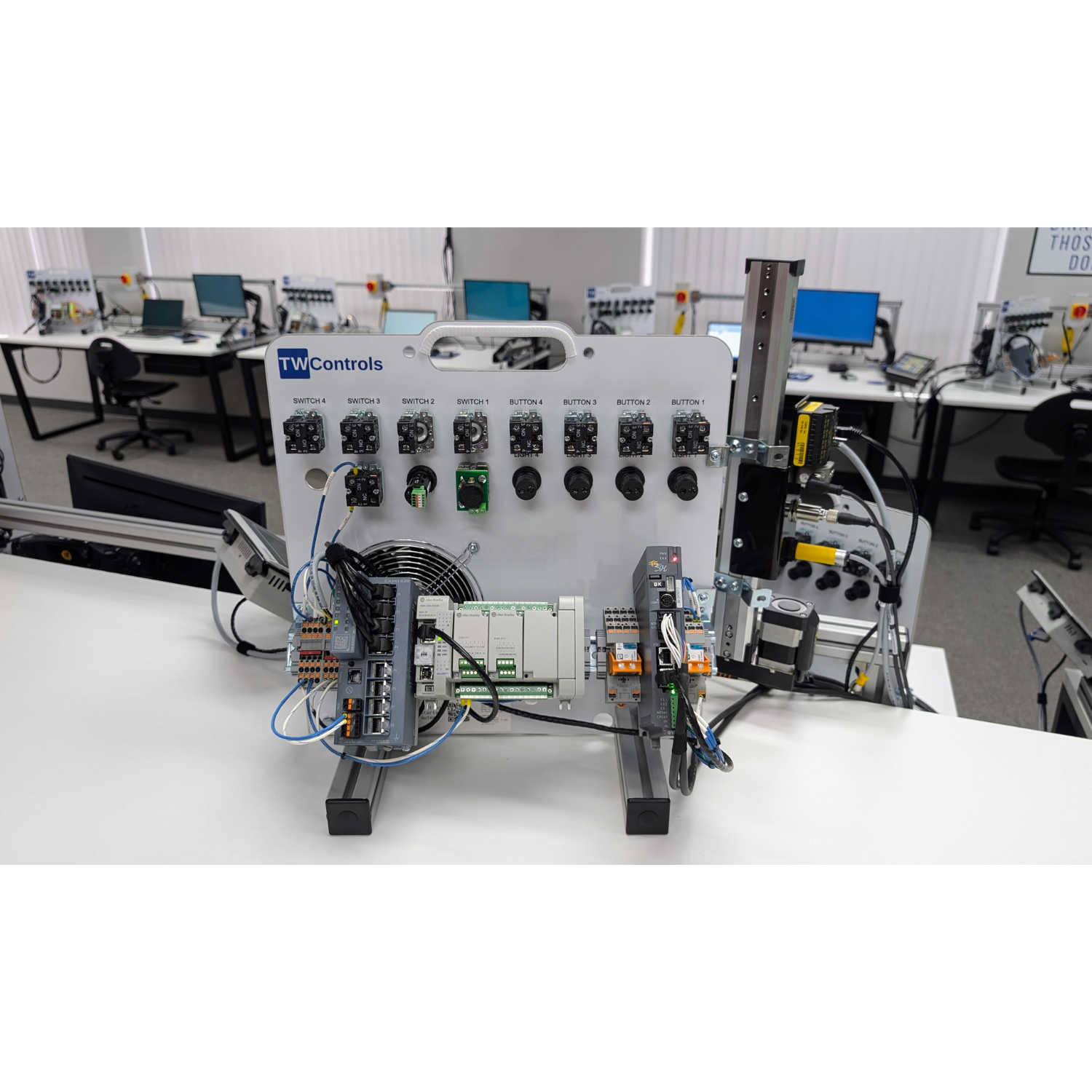
TW Controls - Allen Bradley Micro850 PLC Trainer. The Most Comprehensive for Manufacturing
SKU: TRN-ICP-MICRO850-HMI-LMC-IOLINK
SKU: TRN-ICP-MICRO850-HMI-LMC-IOLINK
SKU: TRN-ICP-MICRO850-HMI-LMC-IOLINK
Our trainers are designed with all of the common control components that you will see on industrial equipment to give you a solid foundation to build your skills on.

Automation equipment can be found in every manufacturing plant in your community, commercial buildings, stoplights, and even amusement park rides.
This is the most comprehensive PLC trainer covering most aspects that you will see in an industrial control panel including:
Allen Bradley Micro850 PLC . Uses Rockwell Automation’s Free Connected Components Workbench Software.
Discrete includes 16 discrete 24VDC inputs and 16 discrete 24VDC outputs.
Analog includes 2 inputs and two outputs, all capable of 4-20mA or 0-10VDC.
Allen Bradley Powerflex 525 Variable Frequency Drive (VFD) is 120VAC wall powered and outputs 230VAC power to the 3 phase motor. Controls can be hardwired or over Ethernet/IP.
Panelview 800 HMI touchscreen which uses the free Connected Components Workbench software to program your operator interface.
Turck IO Link Smart Devices for the factory of tomorrow including an IO Link Master compatible with Ethernet/IP, Modbus TCP, and Profinet, an encoder coupled to the 3 phase motor for closed loop control, and intelligent sensors.
Yamaha Linear Actuator for Motion Control. Using Add On Instructions (AOI), you can have your motion controller integrated in less than 30 minutes. While this is a non-motion PLC, we have lessons to learn the motion instructions used on Kinetix servo controllers.
Siemens Scalance Layer 2 Industrial Managed Ethernet Switch supports advanced networking features including cyber security, Ethernet/IP, Profinet IO, VLAN, and redundancy.
Lesson provided by Tim Wilborne who has made over 1000 instructional videos and has over 100,000 followers.
Click here to view the Online PLC Courses available for your PLC training.
Not only will you learn about the different programming aspects of manufacturing equipment, you will also learn industrial control wiring, installation debugging, and most importantly troubleshooting systems when they don’t work.
These are the same PLC trainers that we use in our classes. Our hands on approach to learning can be replicated in your technical school, college, or in the comfort of your own home.
Benefits
☑️ Increase skills
☑️ Increase employee retention
☑️ Reduce unplanned downtime risk
☑️ Reduce time to repair
☑️ Improve workforce development
☑️ Prepare for the digital transition
Who is this trainer for:
☑️ Maintenance Technicians
☑️ Instrumentation Technicians
☑️ Automation Technicians
☑️ Engineers and Software Developers
☑️ Students in Engineering and Mechatronics
☑️ Anyone who needs cross-training on PLCs
Trainer Features
☑️ 120VAC wall powered
☑️ Portable size for use on table/desk
☑️ Lightweight design
☑️ Optional case for easy transportation
☑️ Free access to online PLC courses
About Us
☑️ Family owned company located in Roanoke, VA
☑️ Established in 2006
☑️ Made in the USA
☑️ Advocates for manufacturing and skilled trades
☑️ Our training center uses these same concepts
What you will learn
PLC and HMI Programming
Downloading, uploading, and going online
Locating I/O tags and devices, tag aliases, forcing I/O, and toggle bits
Basic instructions, timers, and counters
Machine step sequencing methods
Analog scaling and mathematical manipulation
PID Proportional Integral Derivative for process control
Data types and numbering systems
Arrays with 1, 2, and 3 dimensions and manipulating data inside them, indexed/indirect addressing
Add on instructions (AOI) and User Defined Data Types (UDT)
Create and organize a project
Create periodic and event tasks
Common PLC programming languages: Ladder Logic Diagram (LD), Function Block Diagrams (FBD), Structured Text (ST), and Sequential Function Charts (SFC).
Program control JSR, JMP/LBL, FAL
GSV/SSV to get module information, Data/Time, and other advanced diagnostics information.
Password protection
Upgrading and downgrading firmware
Integrating with 3rd party devices
Motion Control for pick and place and industrial robotics applications
Kinetix motion instructions even though this is a non-motion PLC
Can be integrated with cobots
Industrial Control Wiring including AC drives and 3 Phase Motors
Real wire, real terminal screws, and real termination points. You can’t learn to wire UL 508A Industrial Control Panels using 2mm banana plugs
Wiring discrete and analog inputs and outputs, safe for students at 24VDC
Using a multimeter for voltage, amperage, and continuity checks
Reading electrical wiring diagrams and understanding schematic symbols
Sensors, how to wire and the difference between the most common types: photoelectric, inductive proximity, and capacitive
Relays and solid state devices
IO Link., learn about advanced sensors and diagnostics
Basic AC and DC fundamentals
AC drives and 3 phase motors
Powerflex 525 VFD Variable Frequency Drive
AC Induction Motor
Acceleration and deceleration, motor braking, jogging, and protection
Control methods including hardwired start/stop, HOA Hand Off Auto, and Ethernet/IP control
Integrating with PLCs and HMIs
Networking and Cyber Security
Basics of IP address, subnet, and gateway
Configuring your PC to communicate with your PLC over Ethernet
Communicating with remote Ethernet I/O, and distributed I/O
Produced and Consumed tags (between two PLC trainers)
Message Instructions
Realtime data logging and acquisition
Analyze and troubleshoot systems using trend charts
Ethernet/IP in the IO Configuration and Modbus TCP via Add On Instruction (AOI)
Industry 4.0, IIoT, and integrated systems
Remote monitoring and analytics
Alarms and emailing on events
Configuring Ethernet switch, layer 1, layer 2, and layer 3
Industrial Cyber Security
Diagnose and resolve issues with Ethernet switches and devices on a network
Set up one-to-one IP address translation (NAT) for segmenting machine-level network devices from the plant network
DLR Device Level Ring topology for redundancy
Trainers can be interconnected with each other to simulate a manufacturing plant network